Taisun, besides learning to identify operational risks brought about by climate change, also refers to the TCFD (Task Force on Climate-Related Financial Disclosures) recommendations published by the Financial Stability Board (FSB). The company has incorporated the four core disclosure elements – “Governance,” “Strategy,” “Risk Management,” and “Metrics and Targets” – into its operational management. Furthermore, Taisun discloses the impacts of climate change-related risks and opportunities, as well as potential response measures, in its sustainability report.
1. Governance
The ESG Sustainable Development Committee is responsible for overseeing climate-related risk management and approving climate strategies and targets. Climate-related response measures are jointly decided by the ESG Committee and approved by the chief commissioner for implementation. The committee reports to the board of directors annually, with the board monitoring implementation effectiveness.
In 2023, one report was made to the board regarding significant opportunity and risk assessments, including financial risks, product opportunity risks, and carbon fee impacts.
2. Strategy
The company refers to the IPCC’s Sixth Assessment Report (AR6) and the Environmental Protection Administration’s goal of limiting temperature rise to 1.5°C. They use the TCCIP (Taiwan Climate Change Projection Information and Adaptation Knowledge Platform) tools to assess physical risk scenarios. The company has adopted a scenario of limiting global warming to below 2°C for assessing physical and regulatory transition risks.
① Transition Risk∣Policy and Regulatory Risk
The “Climate Change Response Act” will impose carbon fees on high-emission products with direct or indirect emissions starting in 2025, potentially increasing our company’s operational costs, although it won’t impact overall operations. Our company completed greenhouse gas inventory education and training in 2020 and has introduced management approaches such as utility equipment replacement. We plan to establish reasonable and achievable carbon reduction targets in 2024.
After the century’s severe drought, there’s a consensus among political and social sectors regarding the Water Resources Agency’s plan to levy water consumption fees. Our company was included in the “water consumption fee” collection targets in 2022, bringing groundwater into the national charging system. In compliance with government policies, we’re approaching this from water conservation and recycling perspectives, with food safety as the fundamental principle. We’ve begun economizing on product cooling, packing materials improvements, and personnel water usage to reduce water withdrawal.
② Physical Risk∣Immediate
Due to increased extreme weather events, the frequency of typhoons, heavy rains, thunderstorms, and high temperatures has increased. Although our factories are located in central Taiwan near mountainous areas with relatively low probabilities of wind and flood disasters in the past, poor management of oil waste products potentially caused by high temperatures could lead to spontaneous combustion. Sudden storms will also increase operational impacts such as water source purity treatment and equipment damage in the plant area, causing financial losses.
Although our factory equipment and warehouses have little experience with major water disasters, Taisun still prioritizes waste recycling management, preventive maintenance of plant drainage systems and equipment, installation of water and disaster prevention response systems, and increasing and flexibly adjusting storage space. This ensures normal products load-out while also preparing mechanisms to deal with disasters affecting consumer food group customer warehouses and livestock group customers, maintaining operational development and reducing immediate significant risks.
Moreover, extreme climate affects raw material procurement, upstream and downstream transportation interruptions, and personnel safety. We expect this situation to lead to shortterm cost increases in various areas. Our company uses diverse procurement channel cooperation, combined order transportation, transportation route consolidation, and alternative subcontracting to achieve carbon reduction and avoid product and human resource losses.
③ Resource Efficiency Opportunities
In addition to complying with government water resource conservation policies, our company has begun to inquire about water recycling system planning. However, due to equipment system and recycling site factors, the Sustainable Development Committee currently has no optimal solution after evaluation. We expect this case may increase operational costs financially, but in the long run, it’s still an effective solution that is environmentally friendly and gradually reduces clean raw water extraction.
In 2022, our company’s ESG Sustainable Development Committee launched a “TCFD Climate Change-related Financial Disclosure” survey. They convened relevant members in meetings to jointly assess potential risks the company may face due to climate change, identifying risk sources, conducting risk analysis and assessment, and addressing risks to continuously reduce impact. They discussed and identified transition risks (policy and regulations, technology, market, reputation), physical risks (immediate risks, long-term risks), and opportunities (resource efficiency, energy sources, products/services, market, resilience). Considering the time frame, the assessment intervals are short-term (1-3 years), medium-term (3-5 years), and long-term (over 5 years). The top 10 in each interval are prioritized, with short-term risks addressed first. Medium and long-term risks are evaluated based on company resources. Annual reviews of strategic actions assess the effectiveness of target implementation. If necessary, risk discussions and identification are conducted again. In principle, risk management items are reviewed every 3 years for appropriateness.
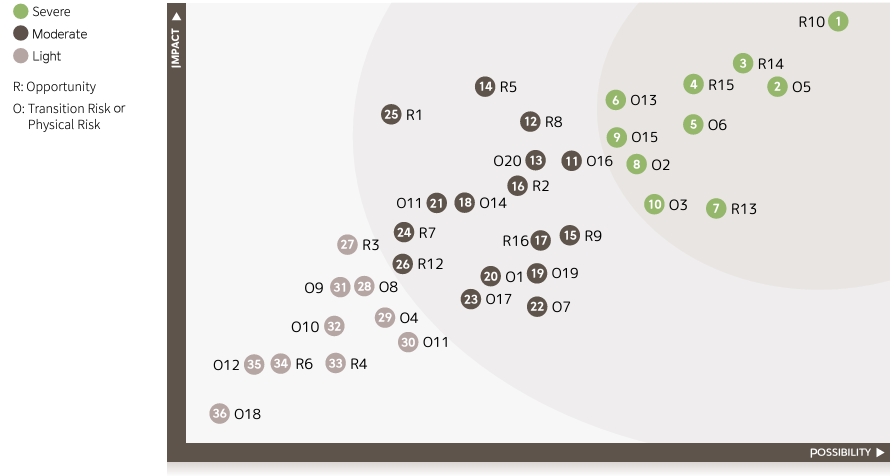
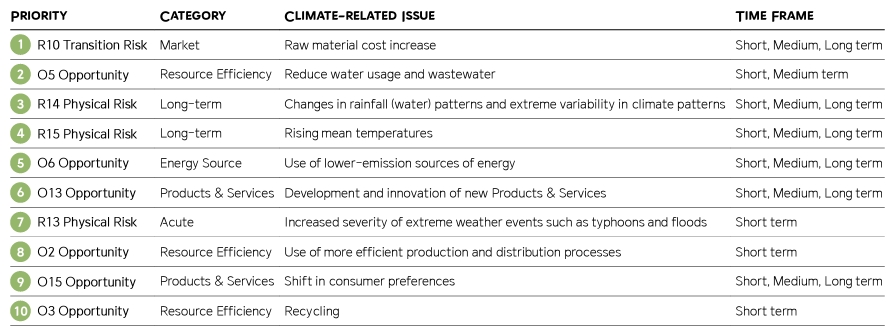
- Since 2020, the company has been conducting annual internal greenhouse gas emission inventories following ISO 14064-1:2018, with third-party verification planned for 2026.
- Annual budgets are allocated for process improvements and equipment updates to reduce energy consumption.
- The company aims to increase the rate of ranch wastewater irrigation for napier grass to 10% by 2026, reducing water treatment usage. The 2023 target of 5% was successfully achieved.
- After implementing water recycling policies in 2023, water withdrawal was reduced by 2%, with a target of 5% reduction by 2026.
- The company has established a management and personnel culture to increase business waste recycling rates, achieving over 95% in 2023 and aiming to maintain this level.